Keep’em Cool
Transporting hogs to packing plants can produce casualties: 0.27% of groups arriving at packing plants were classified as “subject,” based on an earlier study by Cate Dewey, DVM, University of Guelph in Ontario.
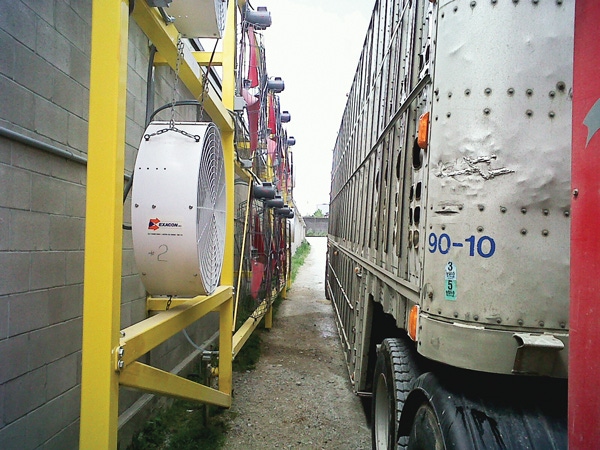
Transporting hogs to packing plants can produce casualties: 0.27% of groups arriving at packing plants were classified as “subject,” based on an earlier study by Cate Dewey, DVM, University of Guelph in Ontario.
Further, of pigs that died in transit, 34% were identified as subject or fatigued prior to death. Dewey’s study classified 6.1% of deaths as occurring at the farm, 30.4% at assembly points and, by a wide majority, 63.4% at the packing plant.
Forty-eight percent of the subject pigs showed severe signs of heat stress or fatigue.
The Canadian research showed that during heat stress, pigs control their body temperature by panting. If this regulating device fails to lower body temperature, then pigs collapse and tend to die of heart failure, says Sam Bradshaw, environmental specialist, Ontario Pork.
Air temperature and relative humidity are carefully monitored and controlled inside hog barns in order to maintain health and performance. But when hogs are in transit, those factors are strictly dependent on outside weather conditions, he says.
“When transport trucks are in a moving mode, air flow created in the trailer causes air circulation and consequently, temperature and relative humidity are similar to outside conditions,” Bradshaw explains.
But when hog trailers stop and park at the plant and wait to be unloaded, air circulation slows and air temperature and humidity can rise, potentially increasing stress on the animals, he points out.
Bradshaw says research indicates that as the waiting time increases by 30 minutes, the risk of pigs dying increases by 2.2 times.
Previous research on pig transport trailers in Ontario during the summer showed that when stopped, trailer temperatures increased on average by 10.8°F.
“It took 56 minutes for the truck to reach its maximum temperature after the stop. Thus, this rise in temperature may be responsible for the correlation between the waiting time in the yard and the risk of death or being a fatigued, subject pig.”
Bradshaw notes the research also concludes that pigs shipped in summer were twice as likely to die in transit from fatigue compared to pigs shipped during other months of the year.
Collaborative Study
The Farm Innovation Project, funded in part through Growing Forward, a Canadian federal-provincial-territorial initiative, was designed in three parts:
1. To erect fan banks at two packing plants in Ontario;
2. To equip specific trailers with temperature and humidity data loggers; and
3. To determine the time it takes to lower temperature and humidity inside the hog trailer to near outside values.
Two banks of fans were designed and erected, one at Quality Meat Packers and one at Conestoga Meat Packers, Bradshaw explains.
Like what you're reading? Subscribe to the National Hog Farmer Weekly Preview newsletter and get the latest news delivered right to your inbox every Monday!
Each fan bank was equipped with eight, 48-in. fans, each delivering 28,000 cu. ft./min. (cfm) for a total of 224,000 cfm, plus four, 36-in. fans, each delivering 12,000 cfm for a total of 48,000 cfm. In all, the fan banks circulated 272,000 cfm, he states.
Some fans were also equipped with misters, which can be effective at reducing temperature and relative humidity (when outside humidity is under 60%), but data is not complete for that segment of the trial.
Data loggers monitoring temperature and relative humidity were installed in seven of 10 hog trailer compartments, Bradshaw says. Three data loggers were placed in each compartment — one temperature logger on each side of each compartment and one temperature and one humidity data logger in the middle of each compartment (Figure 1).
In the trial, two trailers were monitored at Conestoga Meat Packers. The trailers were scheduled to arrive 30 minutes apart. If the outside temperature didn’t exceed 77°F, one trailer would park next to the fan bank with the fans running and wait to unload for at least 30 minutes. The second trailer would wait without the fans for about 30 minutes and then unload the hogs.
At Quality Meat Packers, one trailer was monitored due to the restricted width of the lane leading up to the loading dock.
Preliminary statistical analysis of the data collected in these experiments show:
• Fans are effective in reducing temperatures across most of the compartments. The exception seems to be compartments 5 and 8, where the temperature differential is reduced less than in other compartments (Figure 1).
• Fans are most efficient at reducing the temperature in the parts of compartments closest to the fans.
• The temperature and humidity index are reduced in fan treatments except for compartment 8.
• Initial information indicates that the fan banks remove heat and humidity within 10 minutes from the waiting trailers.
Bradshaw says that overall, the fan treatments are efficient in creating more comfortable conditions in the trailer in terms of temperature and humidity.
About the Author(s)
You May Also Like