Building a Successful Farm Culture
Developing a strong work ethic and teamwork paid off when PRRS came calling to Wakefield Pork Inc. (WPI).
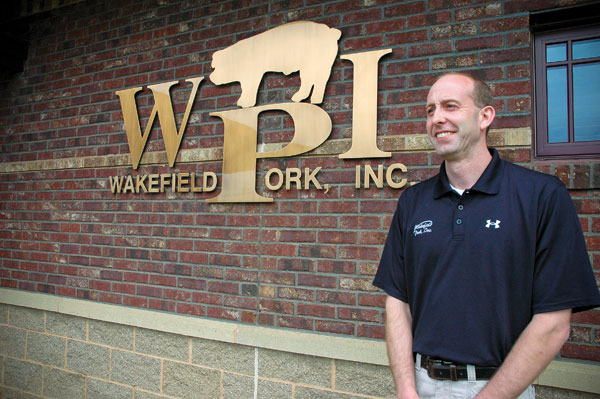
Scott Van Deest learned early on when he went to work for Steve and Mary Langhorst at their 300-sow hog farm in Gaylord, MN, that he’d better be on top of his game if he wanted to stick around for long.
Now, 15 years later, Van Deest has been heralded as the Minnesota Pork Industry’s Swine Manager of the Year (sponsored by Land O’ Lakes). His drive and determination skills have enabled the Peter Marcus Farm he manages at Lafayette, MN, to consistently rank in the top 20% of production performance in the Wakefield Pork Inc. (WPI) system.
WPI is celebrating its 20th anniversary this September. WPI was started as a partnership between Chuck and Joan Peters and Steve and Mary Langhorst.
WPI is comprised of a network of farrow-to-wean operations and 200 contract growers who finish the pigs. There are 250 employees who work in the sow facilities and as field support and office staff.
Starting from Scratch
Van Deest worked at and later managed the Langhorst’s home farm until 2003, when he was tabbed to develop the Peter Marcus Farm. He supervises the 2,400-sow, farrow-to-wean farm that started from scratch in the fall of that year, from overseeing construction to getting the animals in place and starting breeding in January 2004.
Consulting swine veterinarian Paul Yeske recalls how he and Van Deest shared heat detection duties on that first group of gilts on Christmas Eve.
“It was a big step because I went from managing 900 sows (at the Langhorsts) to 2,400 females, and from managing four employees to managing nine employees,” he recalls.
PRRS Challenge
With a new farm startup, expectations for production were high, so when PRRS (porcine reproductive and respiratory syndrome) struck four times in four years (2004 to 2007), management became even more challenging.
“The unfortunate thing was, we would just get back to being PRRS negative and getting good production again, then one or two months later we would break again,” Van Deest says.
These breaks were likely caused by airborne virus, even though this area in south central Minnesota was not saturated with pig operations, says Yeske of the Swine Vet Center at St. Peter, MN.
In 2008, the Peter Marcus Farm became one of the first sow farms of its size in the state to receive air filtration technology, adding to Van Deest’s management challenges.
Van Deest and his team burned through more than a pallet of caulk to seal up all possible air leaks inside and outside the unit.
“We learned that PRRS travels in the air. Fortunately, the filters did the job, along with closely following biosecurity protocols, and we haven’t had a break since,” he says.
But staff naturally wondered if it was all worth it, Van Deest says. A year after the operation was filtered, a graduate student for former University of Minnesota PRRS researcher Scott Dee, DVM, started a project on biosecurity procedures, Yeske explains. The student collected air samples for 10 consecutive days next to the site that Van Deest manages, plus from doorways, employee’s shoes, socks, lunch bags and many other objects to see if the virus was moving around the site.
During this time, the weather was perfect for PRRS transmission — cloudy, hazy, and cool (40-45 °F). A positive PRRS air sample was picked up near the site and on the inside of one of the barn doors, Yeske says.
“We use the ‘bench entry system’ at many Wakefield sow sites, which separates the dirty side from the clean side of the entryway, and the virus was found on the dirty side of the room,” Yeske says. “The virus never made it across to the clean side.”
Biosecurity is always stressed, but these research results made it real for employees, Van Deest says.
“There was a new appreciation for following the biosecurity manual,” adds Mary Langhorst, vice president of Operations and Human Resources for WPI. All visitors to the sow sites are closely monitored. “Logs track everybody who comes and goes; everyone has to sign in if they are going into a unit and fill out a form to assure that animal health protocols are followed.”
Visitors must be away from pigs two or three nights to visit a Wakefield Pork farm, plus their vehicle will be inspected inside and out before they are allowed in, Van Deest says.
“All of the Wakefield facilities follow the same strict health procedures whether they are filtered or not, but the amount of downtime is increased at the filtered farms. But you have to follow all of the biosecurity protocols, because filters are really just one additional piece of the biosecurity plan,” Yeske explains.
Dedication to Management
Van Deest’s farm was chosen for filtration because of his dedication to management, Langhorst says. “We felt that Scott could manage it and make sure we didn’t make management errors that would cause the filters to fail.”
What’s his secret? Van Deest says there are no magic formulas, just ensuring every detail is done right each day and done that way consistently.
“Some people look at it as just working in a pig barn, but I don’t because there is always something different every day. You don’t quit learning, and I even learn from my employees,” he says with an easy smile.
Production success comes by setting goals “to try to be one step better than everybody else, and I’ve got great employees who have the same philosophy that I do to be the best,” Van Deest says.
He keeps that motivation and passion by looking at the big picture. “This isn’t just a job; we are putting food on the table.”
Motivation
Langhorst explains Wakefield Pork has a variety of programs to keep employees energized to excel.
Begun as a one-year effort, a program they call Naspig, fashioned after a NASCAR competition theme, is entering its seventh year, she says. WPI staff competes to win weekly, quarterly and yearly prizes that can reach thousands of dollars for top farm production. PigCHAMP performance records are used for ranking. “It goes even beyond the competition to employees taking pride in their work and being recognized,” Langhorst states.
The program was developed to train new employees on the reasons they perform their tasks, Langhorst says. But it has helped employees understand production records and what the numbers mean as well, Yeske notes.
“The teamwork that has come out of this has helped stabilize farm staffs such as Scott’s,” Langhorst says. The staff at Peter Marcus Farm has a combined 65 years of experience that instills trust that they will get the job done right each time, Van Deest explains.
When new employees of Wakefield Pork need to be motivated and learn about employee management, they are sent to Van Deest’s farm. “We brought new employees for the WPI multiplication system (Little Falls, MN) to Scott’s farm, where they stayed and trained for about two weeks,” Langhorst says.
The difference in the attitude of those employees was obvious when they returned to work at the multiplication unit, Yeske says. “Scott taught them that his staff is very consistent in what they believe and do every day, and that there are no acceptable short cuts.”
Yeske says new employees learn two key elements of management from Van Deest: “They experience what hog production is like, and they experience the farm culture that it takes for a unit to be successful.”
Keeping hog barns clean is one of the biggest employee motivators. “Nobody wants to walk into a dirty barn, because that first impression when you open the door is going to stick with you,” Van Deest says.
Community Activities
The top swine manager also performs beyond his farm job. He serves as a volunteer firefighter and member of the local ambulance crew. He is also a member of the Nicollet County Pork Producers who grilled 20,000 pork chops last year at a variety of area events, including weddings, benefits, customer appreciations and anniversary celebrations.
“Scott has volunteered for anything in the way of extra-curricular activities, and does a great job of showing the community that we care about people, care about what we do at Wakefield Pork Inc., and try to make it a fun place to work,” Langhorst says.
The main office at Gaylord features a large training room that is used by WPI and the city of Gaylord for special community events.
Morale Boosters
Van Deest hangs posters with positive messages all over the farm to inspire others to greatness and to promote teamwork.
The company also inspires its employees with Twins baseball game tickets, off-site retreats and motivational and inspirational speakers for manager meetings. Bonuses are also paid for pigs/sow/year. “Those efforts get people motivated,” Van Deest says.
“We are also very big into the ‘We Care’ program — that we actually care about the hogs that we are raising in a safe work environment — and that they are produced safely for consumers,” Langhorst says.
About the Author(s)
You May Also Like