Tackling intestinal health through a three-team approach
With multiple sow farms, Maschhoff notes comingling pigs adds to the complexity of health statuses within pig flows.
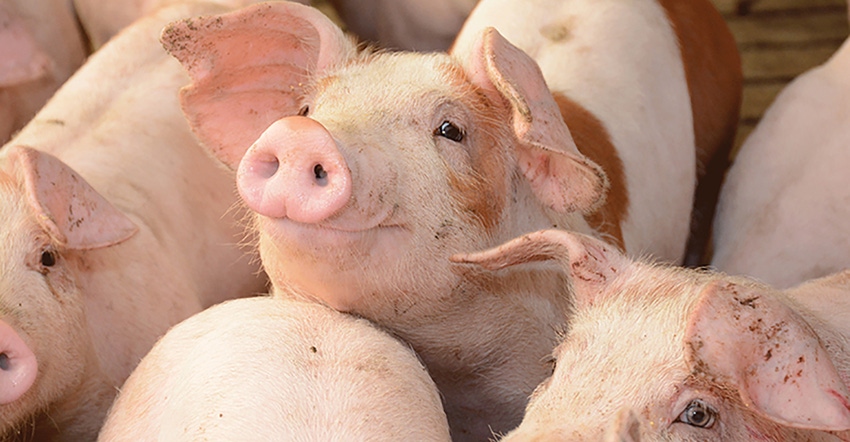
Managing a 120,000-sow base across six states, marketing 4 million hogs per year and overseeing 1,200 employees, The Maschhoffs is a complex swine production system, but Amy Maschhoff says so is the gut of the pig.
"The gut is complex itself, similar to our production systems, and so how we think through that is important, in how we put in protocols or solutions or technologies to be able to control and help our pigs be healthy and grow well," said Maschhoff, who serves as the director of health for the Carlyle, Illinois-based pork production system.
During the recent Kemin Intestinal Health Symposium in Palm Springs, California, Maschhoff noted that due to their production system design, they often put stress on pigs, which can impact intestinal health. But one thing they have learned is that pigs are very resilient.
"I still think there's huge opportunities for us to think about how we continue to do that better in those stressful situations in our production environments today, and I don't want to talk about intestinal health without saying that we've got to continue to do a better job of how we manage the stressful events that happen in our pigs and our production systems," Maschhoff said.
When it comes to intestinal health, The Maschhoffs take a systems approach and have three teams dedicated to it: health, nutrition and operations. For operations, they try to follow a lean manufacturing principle to reduce some of the variability.
"We don't have necessarily cookie cutter design barns or facilities, and so we try to create standard work processes," Maschhoff said. "Whether your barn is in Wyoming or southern Illinois, we still want to recommend that you process pigs and do certain things at the same time, and this helps our system evaluate what are the continuous improvement opportunities that we have, instead of having multiple variations across the system."
Lessons learned from one region may then be applied across the system. In the farrowing room, that could be how detergents, disinfectants and power washer equipment are used. For market barns, that may be consistent downturns, truck washes and sanitation.
With multiple sow farms, Maschhoff notes comingling pigs is common and adds to the complexity with different viruses, bacteria and health statuses within the pig flows. However, the system has its benefits with space utilization, fill time, and support and supply resource management, in areas such as propane and transport.
Labor has also been a challenge for the pork production system.
"When we try to optimize labor at the sow farm level, it's about picking that priority list of what absolutely has to get done in the sow farm and what doesn't have to get done … one of the things that unfortunately comes out of the list, relative to intestinal health when you're optimizing labor of the sow farm, is we may not wash the farrowing house between turns exactly per protocol, which is not ideal from a piglet health perspective," Maschhoff said. "When I look at some of the production partners we work with, raising pigs every day is not necessarily always their first priority depending on the time of year as their individual family operations are complex, too."
One of the ways The Maschhoffs' health team has addressed this is through ease of administration, as well as standard practices and education. With 1,200 employees, safety is also a top concern.
As for nutrition, the swine production system has a partnership with the University of Illinois and the Dr. Mike Ellis lab to evaluate new nutritional technologies before taking them systemwide. Together they examine the application, whether that be dry or liquid, and for what stage of production; the complexity of adding the product; the biological impact on morbidity, mortality and growth; the cost per pig; and the scalability.
"At the end of the day, we use what we call our marginal economic values when we're evaluating nutritional technologies, so what is going to be that cost per pig? We have to have that in mind because those operational metrics are extremely important for us," Maschhoff said. "And then how do we scale this? We have our own company-owned mills, but if we want to put some technology in our system, are we going to coordinate with external toll mills to get that technology implemented?"
To evaluate nutritional technologies on farm, The Maschhoffs have five research centers, three wean-to-market barns and two sow farms. Within that system, 39,000 spaces are dedicated to research and collection of performance data. The research centers have pens and individual scales, electronic feed intake recording capability and can feed up to 16 different diets at one time, with additional blending capabilities as well.
The firm's innovation process also often involves strategic partnerships and external and field research, as well as what Maschhoff refers to as a "business case stage-gate" process.
"When you're looking at innovation from a production system to spec perspective, there's a long list of things you could go want to do and make changes on the system, but you've got to make that priority list of what's going to make the biggest value for us and the biggest changes today, and what things do I have to just keep on the list, that I can't study today or go ask my operations team to try within the business," Maschhoff said.
As for the pork production system's health approach, the veterinarians and herd health team continue to educate and train themselves on infectious diseases, examine how they can approach health issues at scale and try to continue to make good clinical evaluations. It also involves taking into consideration the history of the herd and the animals' response to treatment as well as the individual farm's biosecurity and environment.
"Every environment is different. We talk in our system a lot about what we call the big four: feed, water, air and care and the air in one barn is always different than the air in the other barn, and how we ventilate our barns is extremely important and different, and so taking the environment into account and what influences that had on intestinal health, and just health in general is important," Maschhoff said.
One area that continues to be a challenge for the health production team is disease differentials. The list keeps getting longer with emerging enteric pathogens such as porcine adenovirus and porcine bocavirus being added routinely. Maschhoff said with the ability to detect different viruses, whether it be for whole genome sequencing or new PCR technologies, the differential list keeps growing. Surveillance and prioritization of pathogens is also a challenge.
"I think that one of the challenges that you'll see within a production system is going through and organizing, which one of those goes on my priority list and the highest today," Maschhoff said. "We've done a pretty good job amongst our team, for example, of agreeing on what that prioritization list looks like."
For example, a few years ago the health team examined their finishing mortality and found Mycoplasma hyopneumoniae was an issue and took a system-wide approach to attack the pathogen.
Maschhoff said prevention, control and treatment is key to the pork production system's health approach and they continually try to fine-tune their biosecurity protocols, acclimation processes, vaccination timings and use of antimicrobials, anthelmintics, antiseptics and disinfectants.
Even with their three-pronged approach to intestinal health with standard work protocols systemwide, Maschhoff noted the system is far from perfect.
"Everybody's good at making their own variations of what they think works, compared to what the protocol is, and so I think that whether it's our research team or operations team or health team, we know that what we have on paper isn't always the reality of what happens in barns on a day-to-day basis," Maschhoff said. "An example I can give to you is just cross fostering of piglets. We will tell farms not to move piglets from one sow to the other, but there has not been a day that I have walked a farm where piglets are not moving from one sow to the other because the team thinks they're trying to do the best for the piglet, but they're actually causing more intestinal problems and/or health issues with the piglet by moving them around."
As for future opportunities in intestinal health, Maschhoff has her eye on how to get more Grade A piglets per sow, improve water quality, tackle 0–6-week mortality, enhance facilities, utilize genetics and better manage the microbiome. However, she acknowledges any new approach to the system will need to be multipronged and applicable in the field.
"Making sure that anything that we want to implement in our system is applicable in the field and that you can see it on the production metrics at the end of the day," Maschhoff said. "There's a lot of things that you hear or see, but if you can't apply it in the field and you can't see the results on the metrics, it can't be done in our system and we're not going to adapt it."
About the Author(s)
You May Also Like