Study goes to pig barns to find actual energy use
Research Review: Opportunities exist for reducing fossil energy consumption but differ for each production phase. Therefore, this study is one of the first to specifically measure the energy consumption of operating commercial pork production systems.
December 27, 2017
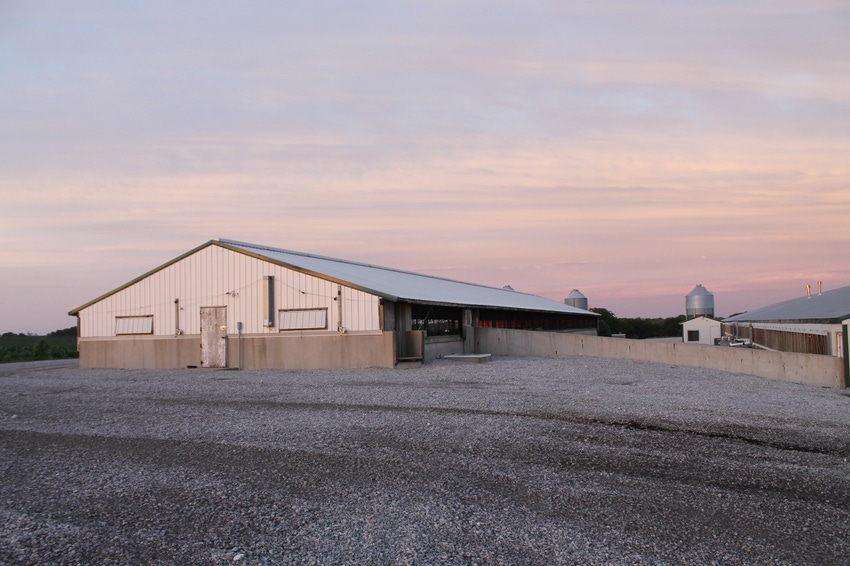
Researchers: Eric Buchanan, Kirsten Sharpe, Lee Johnston, Ph.D., Michael Reese and Joel Tallaksen, Ph.D., University of Minnesota’s West Central Research and Outreach Center in Morris.
Efficiency in today’s hog operation is the name of the game, and that isn’t just for the production of the pigs in the barns. Producers are also concerned about energy use.
The multiple phases of hog production — breed-to-wean, nursery and finishing — each require differing fossil fuel inputs. Sows require extensive cooling during the summer, which is often supplied by exhaust fans, hanging fans and evaporative cool cells. Piglets require extensive heating, especially during the first week of life, which is supplied by propane heaters and heat lamps. In the nursery phase, pigs require both heating and cooling, provided by propane heaters and fans, respectively. Pigs in the finishing phase typically require year-round cooling due to internal heat gains from body heat.
The study’s purpose was to determine actual baseline energy consumption for commercial pork production systems in the Upper Midwest. Previous studies on energy use in these systems were theoretical, relying on scientific literature and brief audits.
Information on how much energy is used, and on the relative amounts of energy used for each purpose is far from complete, and the differences among production units can be large (Barber et al., 1998).
Opportunities exist for reducing fossil energy consumption but differ for each production phase. Therefore, this study is one of the first to specifically measure energy consumption of operating commercial pork production systems and the various loads within these operations, providing data that gives insight into lowering fossil fuel inputs.
To collect baseline energy data, two commercial facilities from west-central Minnesota representing typical Upper Midwest swine production systems were selected for each phase of production: two breed-to-wean barns (BWA and BWB), two nursery barns (NBA and NBB), and two finishing barns (FBA and FBB).
6 barns under study
Researchers at each facility recorded and analyzed monthly consumption of electricity and heating fuel, along with recording monthly pig inventories and production.
1. BWA was a 2,600-sow facility. The farrowing rooms contained 424 stalls and were power-ventilated. Gestation rooms housed sows in individual stalls and were power-ventilated or equipped with curtain sidewalls. The floors were fully slatted, with shallow manure pits and scrapers. Other rooms were used for pressure washers, mechanical equipment, washrooms and storage. The unit had a central office with showers, bathrooms, laundry area and a kitchen. Lastly, a gilt developer unit was commissioned in 2015 and was dedicated to providing replacement gilts to the main sow unit.
2. BWB was a 3,300-sow facility. Farrowing rooms were power-ventilated and had farrowing stalls. The gestation room housed sows in individual stalls and was tunnel-ventilated in the summer and power-ventilated in the winter. The floors were fully slatted over deep manure pits. The unit had several miscellaneous rooms that served as a pressure washer room, storage rooms, work room, and refrigerator and washrooms. The unit had a central office area with showers, bathrooms, laundry area and a kitchen. During late-June 2015, a new GDU was added to provide replacement gilts for the main gestation unit.
3. NBA was a 3,000-head, power-ventilated facility. Three nursery rooms housed 1,000 pigs each and had fully-slatted floors over deep manure pits. The unit also had a load-out and storage area, office and laundry area, and a shower room.
4. NBB was a 10,200-head, power-ventilated facility with fully-slatted floors over deep manure pits. Other rooms included a pressure washer room, mechanical room and storage room. A central office had showers, a bathroom, laundry area and kitchen.
5. FBA was a 2,400-head, tunnel-ventilated facility. Two finishing rooms housed 1,200 pigs each and had fully-slatted floors. The unit had a load-out and storage area, office and laundry area, and a shower room.
6. FBB was a 1,060-head, curtain-sided facility. Two finishing rooms housed 530 pigs each and had fully-slatted floors. The unit also had a central storage room and pressure-washer room and a loadout hallway.
In each swine facility, data were collected from two general categories of energy used in pork production: electrical energy and thermal energy provided by heating fuel (propane).
Researchers measured the energy used by loads directly related to the pigs. To determine if these loads were being monitored, researchers compared the monthly data recorded by sensors in the barn in kilowatt-hours to the electricity provider’s billed kWh used per month.
In some facilities where the collected data did not represent the entire barn, researchers measured loads that were not directly related to pigs, such as outbuildings not related to the production units, but powered from the same utility meter. Researchers monitored these circuits separately to subtract the usage of these outbuilding loads from the swine barn data.
Researchers looked at energy usage of the feed system, lighting, ventilation, manure system, heaters, pressure washer, curtains, heat lamps, controllers, human use, GDU and miscellaneous loads (hallway heaters and lights, workrooms, etc.)
Results
BWA and BWB. Electrical and thermal energy costs were calculated using an electricity price of 10 cents per kWh for both years (average price per kWh across the Midwest) and a propane price of $1.21 per gallon in 2015 and $1.20 in 2016 (using the average price per gallon across all units in this study). The kWh used per pig and the associated costs per pig remained fairly constant over 2015 and 2016. This can be expected, as electricity is used to maintain production and facility management throughout the building, and to power fixed and constant loads. Both facilities used comparable amounts of electrical energy to produce one weaned piglet, regardless of barn size and structure.
Tables with electric and thermal consumption and total costs per weaned pig and feeder pig across the BWA, BWB, NBA and NBB will appear with the complete article at nationalhogfarmer.com.
The largest electric load across both units was heat lamps followed by miscellaneous loads. Heat lamps accounted for about 50% of the total electricity. Miscellaneous loads are the difference between the barn’s utility electric meter and the total of all loads monitored during this study.
NBA and NBB. The kWh use per pig and associated costs per pig were fairly constant over the course of 2015 and 2016. Both facilities used comparable amounts of electrical energy to produce one feeder pig regardless of barn structure and the fact that NBB was four times as large as NBA.
The largest electricity load for both units was ventilation, accounting for 40% of the nursery barn’s consumption. Miscellaneous loads were the next biggest user. At NBA, a shed had several smaller electrical loads and a backup generator with an engine block heater. It contributed to the large miscellaneous loads for this nursery. Monitoring an engine block heater at another site revealed it can use up to 36 kWh per day.
FBA and FBB. Since FBA was tunnel-ventilated and FBB was curtain-sided, FBA was expected to use more electricity due to the increased ventilation.
Also, FBB had a slight rise in electricity use from 2015 to 2016. This can be attributed to the fact that during 2016, the pigs entered the barn at a lower weight, which required heater fans to be used more for the smaller pigs. Another time FBB saw a rise in electricity use was May 2015 to March 2016, when a pit fan motor didn’t work. When fixed, ventilation rose.
See the table on Page 18 for the breakdown of electric and thermal consumption and costs per finished hog across both the FBA and FBB.
FBB used slightly more propane per market pig than FBA. This was expected since FBB was curtain-sided. Also, FBB’s propane use was higher in 2016 than 2015 — again due to pigs at a lower weight than in 2015.
The largest electric load across both units was for ventilation, which consumed over 50%. For FBA, an additional shed on-site was powered from the same utility meter. The shed had several smaller electrical loads and a generator engine block heater.
Comparing other studies
The findings from this study are comparable to other measures reported by industry sources. Anecdotal evidence from a breed-to-wean production system of 70,000 sows indicates average electrical use per weaned pig was 9.7 kWh across the system. Sow units within this system ranged from 5 to 12 kWh per weaned pig.
The most efficient unit had recently focused on improving electrical efficiency. Comparing these industry observations to the current study, where electrical use ranged from 11.27 to 12.18 kWh per weaned pig produced, the current findings are comparable with industry observations.
Nursery findings from this study are also comparable to other industry measures. Brumm (2015) reported industry measures of about 1.8 kWh and 0.31 gallon of propane per feeder pig produced.
These observations are similar to the current findings, which ranged from 2 to 2.49 kWh and from 0.38 to 0.44 gallon of propane per feeder pig produced.
For finishing barns, Brumm (2015) reported electricity consumption of 11.2 kWh per finished pig produced in a tunnel-ventilated barn.
In the current study, electrical use ranged from 13.53 to 15.43 kWh at FBA. The differences may arise from factors such as overventilation (especially during the winter), additional space heating or geographical location.
This study provides a glimpse of where electricity is used in commercial swine barns after it passes through the utility’s meter. Results of this study will help producers and researchers identify areas of commercial pork production that can be improved to increase energy efficiency and profitability.
Researchers: Eric Buchanan, Kirsten Sharpe, Lee Johnston, Ph.D., Michael Reese and Joel Tallaksen, Ph.D., University of Minnesota’s West Central Research and Outreach Center in Morris. A special acknowledgment goes to Anderson Farms, Hillside Hogs, Moore Lean and Moser Farms. Funding for this project was provided by the Minnesota Environment and Natural Resources Trust Fund as recommended by the Legislative-Citizen Commission on Minnesota Resources.
You May Also Like